CO2 refrigerant pump from HERMETIC part of CTES proof of concept
PhD project “Development of cold thermal energy storage units for industrial refrigeration” successfully concluded.
In 2019, HERMETIC-Pumpen GmbH, a world leader in developing and manufacturing canned motor pumps, donated a hermetic high-pressure pump for the refrigerant CO2 as part of a PhD research project at the Norwegian University of Science and Technology (NTNU). The refrigerant pump was installed in an experimental pilot plant to investigate cold thermal energy storage (CTES) in conjunction with industrial refrigeration systems. The research project was conducted by SINTEF Energy Research in cooperation with the NTNU. The experiments performed in the pilot plant have provided the proof of concept for the technology. Under demanding research conditions, the HERMETIC pump proved its performance capability and ensured reliable distribution of the refrigerant in the pilot plant.
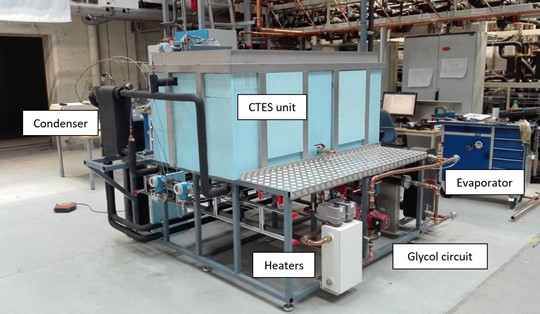
Experimental pilot plant with pump circulation CO2 as refrigerant. (photographic material: SINTEF Energy Research, www.sintef.no)
The impetus of the doctoral project, “Development of cold thermal energy storage units for industrial refrigeration”, is the fact that today refrigeration systems must be designed for the highest occurring cooling load, also referred to as peak load. Many processes that require larger refrigeration systems are batch processes, such as the freezing of food products. Consequently, the peak load only occurs for a brief period of time and most of the time, the refrigeration system works in the partial load range. Introducing thermal cold storage units into these systems makes it possible to shift the provision of refrigeration into the light-load times; this means that planners can dimension the refrigeration system closer to the average load, rather than closer to peak load. In particular, there is major potential for this technology in plants where significant differences occur in cooling requirements in the course of the day, such as large-scale air conditioning and food processing operations.
Proof of concept provided: Use of CO2 for loading and offloading a cold thermal energy storage unit with a phase change material (PCM)
The research project included development of an innovative CTES unit with special type heat exchangers (pillow heat exchangers) and an experimental pilot plant was built, for which CO2 in pump circulation was used as the refrigerant. The technology is based on utilization of the refrigerant CO2 for loading and offloading the cold thermal energy storage unit with different phase change materials (PCM). During the loading process of the CTES system, heat is transferred from the PCM to the evaporating CO2. The PCM solidifies in this process, in other words the relatively high latent thermal energy is withdrawn from the storage unit. When the CTES unit supports the refrigeration system, heat transfer occurs from the CO2 (liquefied) to the PCM (melted). The experiments performed in the pilot plant have provided the proof of concept of the technology. The project demonstrated that effective and compact cold thermal energy storage with PCM is possible in conjunction with condensation and evaporation of CO2 refrigerant. Multiple PCMs were tested in order to meet the temperature requirements of different refrigeration applications. For air conditioning systems, water/ice is an attractive, natural and inexpensive candidate, which was tested in the pilot plant. Finally, a commercial low-temperature PCM (–10 °C) that is suitable for food processing plants, was also demonstrated.
Refrigerant in pump circulation: Rigorous requirements imposed on pumped CO2
A pumped refrigerant is suitable for this application, since the liquid refrigerant must be distributed uniformly in the special heat exchanger plates of the newly developed cold thermal energy storage unit. CO2’s critical point is 31 °C and for heat dissipation, this critical point requires pressures that are much higher than the temperatures frequently used for industrial cooling. The components used must be able to meet these requirements. In the pilot plant, the refrigerant CO2 circulates at a temperature range from 5 °C to –50 °C with a maximum nominal pressure of 52 bar. In addition to effectively dealing with the pressure, the low viscosity of CO2 was also a challenge for the load capacity of the plain bearings. In addition, absolute leakproofness and a low MTBF value, in other words, the highest reliability, is required of the pump that is used.
Reliable refrigerant circulation under demanding test conditions
HERMETIC provided a CAMh2 series CO2 pump. As a high-pressure design, the canned motor pump is optimally adapted to existing plant conditions. This series has been specially developed for CO2 applications in order to meet the requirements of 52 bar operation and standstill pressure.
The research team gave the pump donated by HERMETIC outstanding marks, particularly in light of the demanding conditions in an experimental pilot plant. For example, compared to industrial applications, the pump was confronted with more frequent start-stop cycles, changing operating pressures and changing flow rates. Throughout the entire test, the pump ran with no problems, no leaks, and it ensured reliable distribution of the refrigerant in the pilot plant.
HERMETIC CAMh pump offers design safety and high MTBF values
Canned motor pumps offer design safety due to their absolute leak-free construction and high MTBF values, achieved by eliminating wear-prone shaft seals and couplings. This pump technology uses plain bearings that are lubricated by the refrigerant. The issue is the low viscosity of liquefied gases such as CO2 that continues to decrease with increasing temperature and has a negative effect on the load capacity of the plain bearings. The wrong bearing materials or a surface that is too small cause mixed friction in operation. The results are wear and pump failure. Generously dimensioned HERMETIC plain bearings, made of state-of-the-art sintered materials, ensure non-contact operation and thus pump operation that is virtually wear-free. The construction and choice of materials for the CAMh pump series reliably meet the requirements imposed by the nominal pressure of PN 52. For example, pressure containing parts are made of cast steel. A pressure test at 78 bar is carried out on each pump in accordance with applicable standards such as ISO 15783 for canned motor pumps. In addition, the secondary containment was tested for leaks with nitrogen (N2). With secondary containment, the HERMETIC pump ensures a reliable and controlled flow of refrigerant in the pilot plant.
General operating data of the CAMh series:
- Operating temperatures: –50 °C to +10 °C
- Pump capacity: 1 m³/h to 14 m³/h
- Pump head: up to 85 m
- Nominal pressure: 52 bar
- Test pressure: 78 bar
- Motor power: 3 kW to 7.4 kW
- Plain bearing material: 1.4571/W5 – 1.4571/SiC30
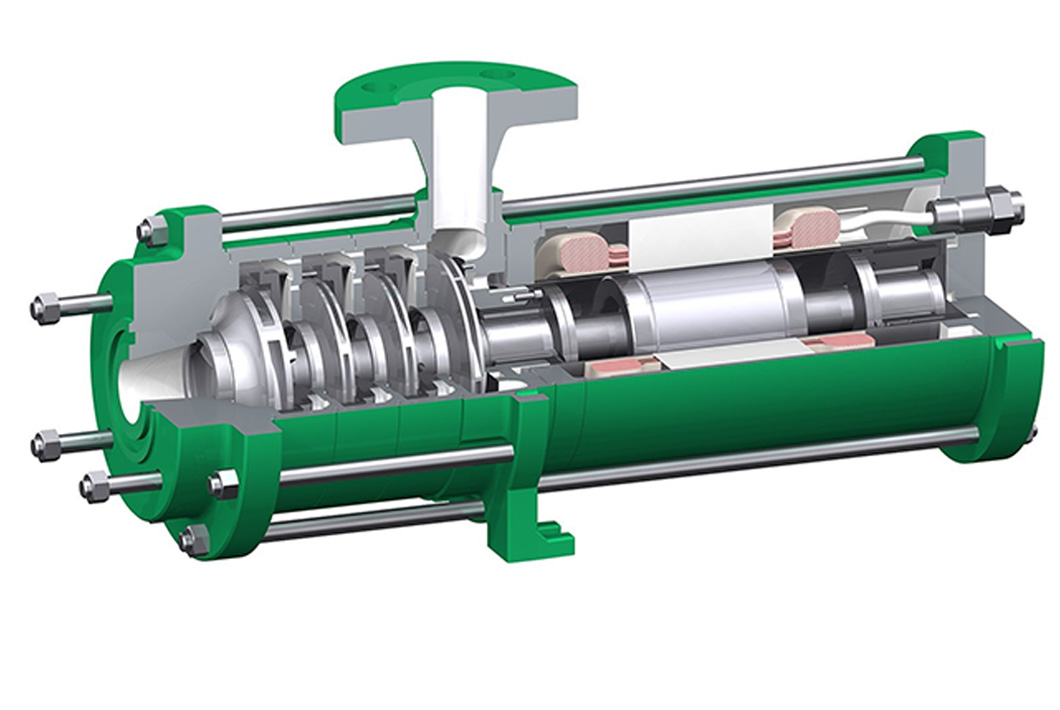
Additional technical information concerning the CAMh series is available here.
Interest in CTES technology is increasing both in industry and the academic sector. Several research projects on this topic are currently underway in the research group. The next step for SINTEF/NTNU is to set up a demo pilot in an industrial refrigeration system.
References to the published research work (conference papers and articles in scientific journals) concerning the experimental tests are provided at these links:
Development of the CTES unit:
sintef.brage.unit.no
Results of the test with water as PCM:
www.sciencedirect.com
iifiir.org
Results of the test with a commercial low-temperature PCM:
www.sciencedirect.com
iifiir.org
Photographic material
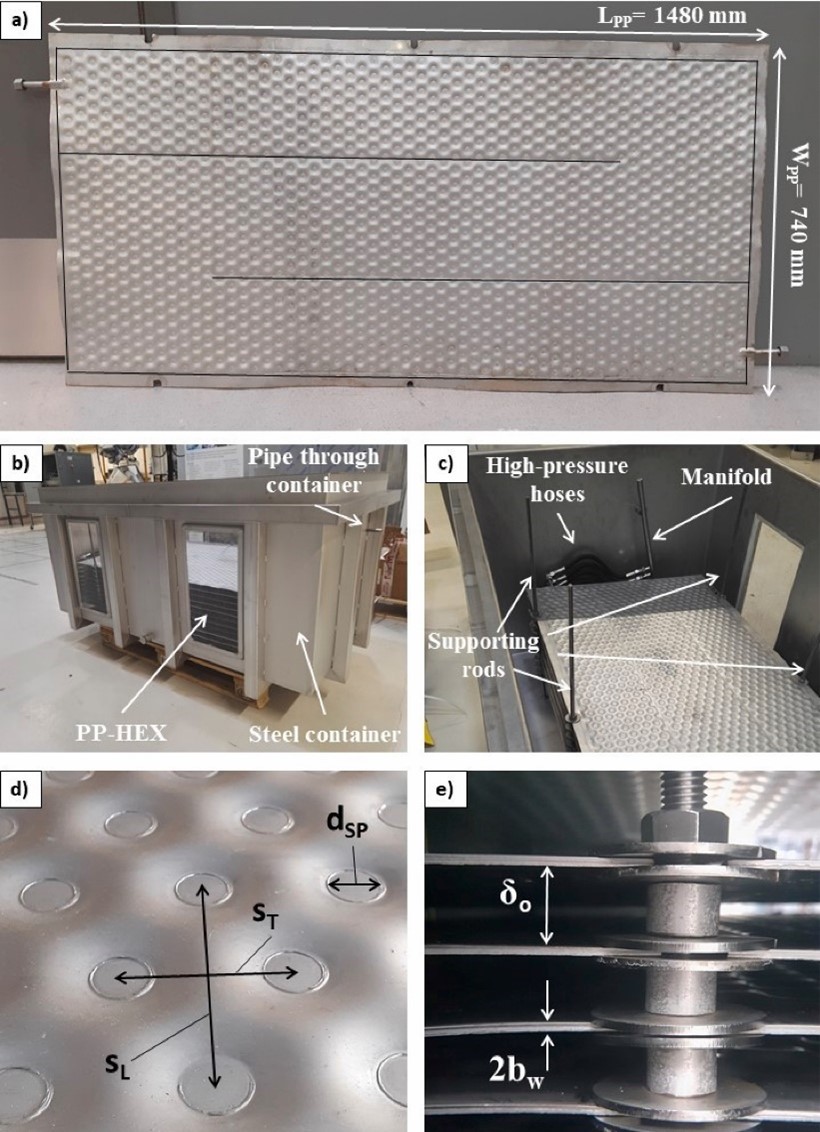
Overview of the innovative CTES unit developed as part of the research project. The figures show (a) a pillow plate for CO2 cooling with inlet/outlet pipes and weld seams marked with black lines (b) the CTES unit prior to assembly in the pilot plant (c) view of the pillow plate heat exchanger inside the tank (d) the corrugated pillow plate surface with the parameters of the welding pattern (e) the stack of pillow plates in the CTES unit with vertical plate division. (Photographic material: SINTEF Energy Research, www.sintef.no)
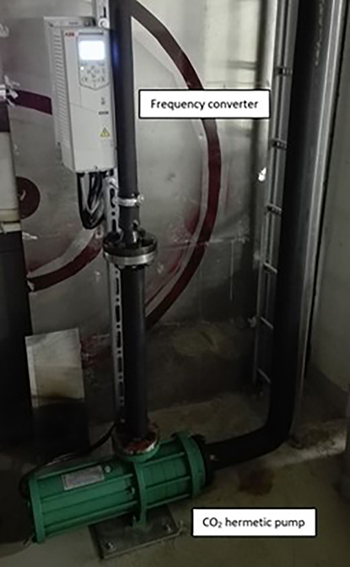
Multistage HERMETIC series CAMh canned motor pump that is used in the pilot plant and which is equipped with a speed-regulated drive. (Photographic material: SINTEF Energy Research, www.sintef.no)
About SINTEF
SINTEF is a broad-based, multidisciplinary research organisation with international top-level expertise in the fields of technology, the natural sciences, medicine and the social sciences. SINTEF was founded in 1950 by the former Norwegian Institute for Technology, which today is part of the University of Norway (NTNU). Through its own growth and mergers with other institutes SINTEF has become one of the largest independent research organizations in Europe. SINTEF conducts contract R&D as a partner for the private and public sectors. There is close collaboration with NTNU (www.ntnu.no). More information is available at: www.sintef.no
Contact
For more information, please contact:
Christoph Galli
Gewerbestr. 51
79194 Gundelfingen
Tel.: +49 761 5830-411
galli.christoph@hermetic-pumpen.com
www.hermetic-pumpen.com
Contact
For more information, please contact:
Christoph Galli
Gewerbestr. 51
79194 Gundelfingen
Phone.: +49 761 5830-411
galli.christoph@hermetic-pumpen.com
www.hermetic-pumpen.com