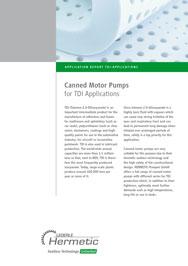
Canned Motor Pumps for TDI Applications
TDI (Toluene-2.4-DiIsocyanate) is an important intermediate product for the manufacture of adhesives and foams for mattresses and upholstery (such as car seats), polyurethanes (such as shoe soles), elastomers, coatings and high-quality paints for use in the automotive industry, for aircraft or locomotive paintwork. TDI is also used in lubricant production. The world-wide annual capacities are more than 1.5 million tons so that, next to MDI, TDI is therefore the most frequently produced isocyanate. Today, large-scale plants produce around 100,000 tons per year or more of it.
Since toluene-2.4-diisocyanate is a highly toxic fluid with vapours which can cause very strong irritation of the eyes and respiratory tract and can lead to permanent lung damage when inhaled over prolonged periods of time, safety is a top priority for this application.
Canned motor pumps are very suitable for this purpose due to their hermetic sealless technology and the high safety of the constructional design. HERMETIC-Pumpen GmbH offers a full range of canned motor pumps with different series for TDI production which, in addition to their tightness, optimally meet further demands such as high temperatures, long life or use in tanks.
TDI is produced from a reaction between primary amines or their derivates, frequently TDA (2.4-diaminotoluene) and phosgene. Due to the toxicity of the parent substances, these are manufactured in the same process. The media used in all processes are carbon monoxide, chlorine, toluene-diamine and dichlorobenzene.
Phosgene: Phosgene is produced by the mixing of the gaseous substances chlorine and carbon monoxide, the activation energy of which must be reduced by the activated carbon catalyst. To avoid dissociation, i.e. separation, of the mixture, a separation temperature of well below 100 °C must be ensured. The phosgene won in this way is dissolved in cold ortho-dichlorbenzene (ODB).
TDA: The toluene substance which is formed during cracking is first nitrified by adding nitrate and then hydrogenized by adding hydrogen. The resulting TDA is then melted at 140 °C and mixed with hot ODB.
TDI: The production of TDI can be divided into 2 phases. The process begins with a cold phosgenization, and exothermic reaction, and ends with the hot phosgenization which is endothermic.
The cold phosgenization
In the cold phosgenization, the hot TDA-ODB solution is stirred into the cold phosgene-ODB solution at low pressure (1–2 bar) or high pressure (up to 20 bar). In a reference plant, this step is performed at 300 °C which increases the energy efficiency of the plant. About 80 % less ODB and about 40 % less phosgene are needed due to the high temperature. The resulting suspension very quickly forms solids. In order to avoid this, various devices exist such as a circulating pump system, counterflow mixing chambers, centrifugal pumps, Venturi mixing nozzles and other mixing devices.
The hot phosgenization
Then the so-called hot phosgenization takes place. Hereby, heat and phosgene are added to the suspension until a clear liquid and no further hydrogen chloride is produced. In this process step, a liquid raw material (approx. 15 % TDI, 80 % ODB, 5 % phosgene), hydrogen chloride vapour and other residues are produced. Hydrogen chloride vapour is corrosive and special alloys with a nickel content are required to protect the apparatuses. Mixing the gas with water forms hydrochloric acid. Hydrogen chloride is then mixed with 18 %-hydrochloric acid to obtain a 30 %-hydrochloric acid.
The liquid raw material is broken down into different constituent parts by various distillation steps in a rectification column. ODB and phosgene are fed back into the process. Ancillaries are cleaned from the TDI in the last column. The distillations are performed in a vacuum.
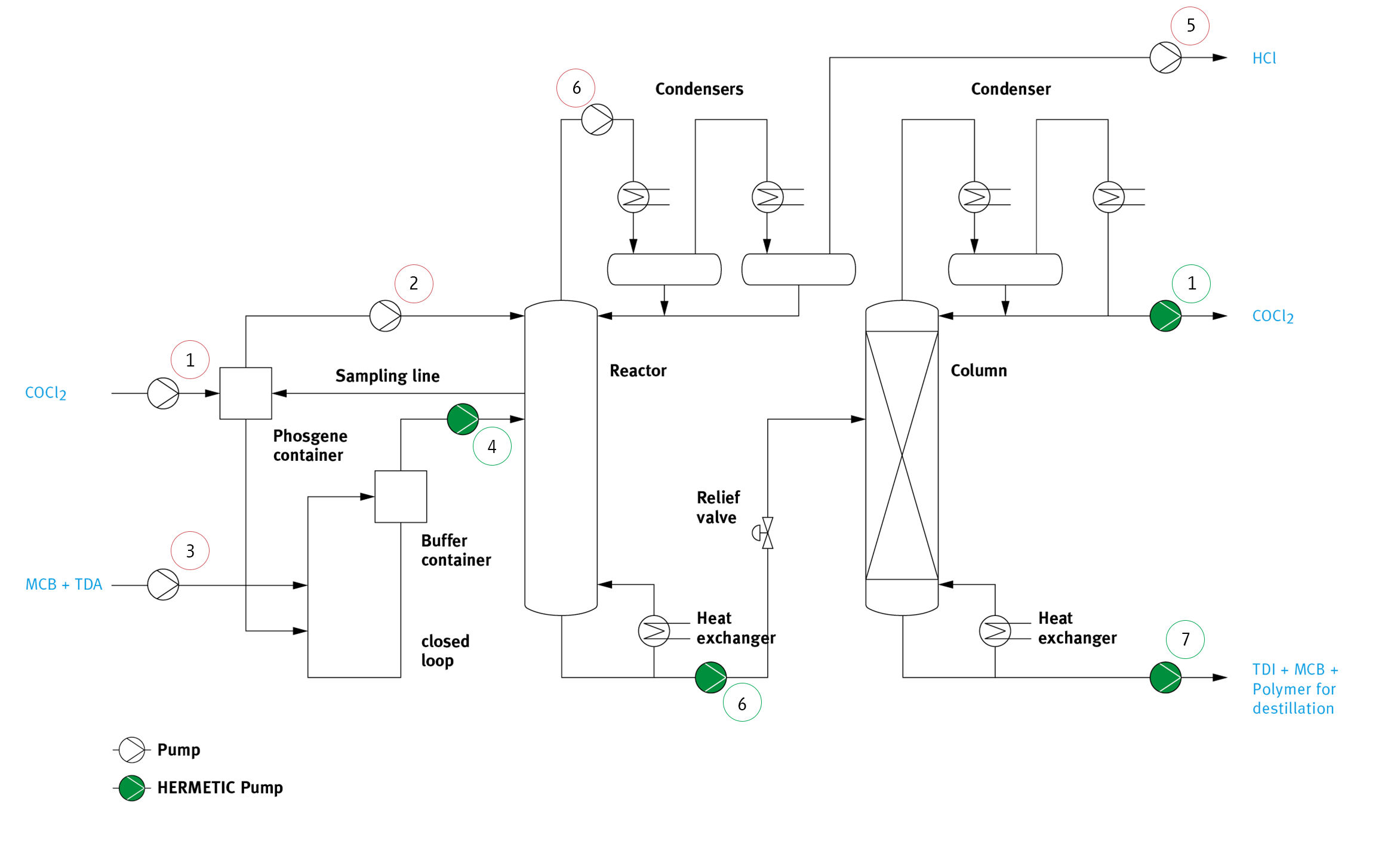
Fig. 1: Toluenediisocyanate manufacturing process
High demands on the pumping technology
Pumps are used in different places in this complex manufacturing process:
- Feeding phosgene (20 bar up to 300 °C) to the ODB solution
- Feeding phosgene and ODB (20 bar up to 300 °C) into the reactor
- Feeding TDA (20 bar up to 300 °C) to the ODB solution
- Feeding TDA and ODB (20 bar up to 300 °C) into the reactor
- Discharging the hydrogen chloride (up to 300 °C) from the reactor
- Discharging the raw material (up to 300 °C) from the reactor
- Feeding/discharging TDI (up to 300 °C) to / from the columns
Since TDI is a health-hazardous, highly toxic substance, absolute tightness from the outside atmosphere when conveying by the pumps is essential. In addition, process temperatures of up to 300 °C as well as the aggressive, corrosive properties of the intermediate products concerned or the application in tanks are further challenges that the equipment has to face. Canned motor pumps are very suitable for this purpose due to their hermetic sealless technology and the high safety of the constructional design.
Leakage-free, safe pump solution for different process steps
HERMETIC canned motor pumps isolate the pumped medium from the atmosphere by a double safety jacket. The terminal box and the cable glands are also gas and liquid-tight and designed for the rated pressure of the unit. Hazardous substances will not escape into the atmosphere if the rotor lining is destroyed, for example, by bearing damage or corrosion. Canned motor pumps therefore offer the best possible safety when handling TDI. Canned motor pumps are used at many different places in the manufacturing process. In this process, HERMETIC pumps are located at position no. 1, 4, 6 and 7. In this article, we deal with the pumps no. 1, 4 and 6 in more detail
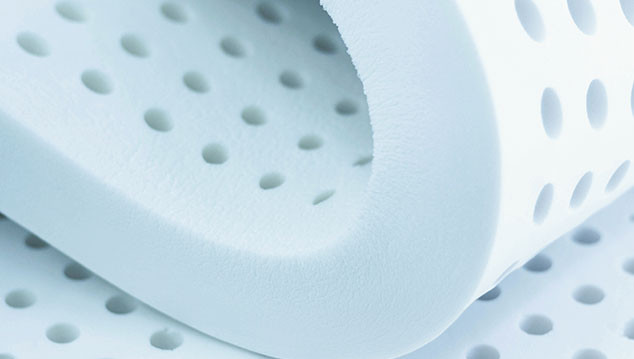
Feeding phosgene to the ODB solution (No. 1)
In a reference plant, a single-stage HERMETIC canned motor pump of the TCN type is used for feeding phosgene to the ODB solution. This series is particularly suitable for safe pumping of aggressive, toxic, hot, explosive, valuable and inflammable liquids and liquified gases. The pump is designed for use in fuel depots, terminals, chemical and offshore plants, gas storage caverns and industrial plants. In conjunction with different installation systems, the pumps of this series which are available both as TCN (single-stage) and TCAM (multi-stage) are the optimum pumps for these application cases.
In addition to the double safety jacket, they also achieve best marks in terms of long service life. This is because the hermetic design requires the bearings to be assembled in the operating liquid. Therefore, only hydrodynamic slide bearings are normally used. When operated correctly, these have the advantage that there is no contact between the bearing sliding surfaces. They are therefore wear and maintenance-free in continuous operation. Service lives of more than 10 years for hermetic pumps are not uncommon.
In addition, the canned motor submersible pumps offer clear advantages regarding installation space thanks to their relatively compact dimensions in comparison with conventional pumps with a face seal and magnet-coupled submersible pumps. Because the long drive shaft is omitted in canned motor submersible pumps depending on the immersion depth. The rotating parts of the pump shaft are located in the canned motor pump and are accordingly short. The pump is suspended from a static supporting tube that is mounted on the manhole cover. Apart from holding the pump, the supporting tube only has the task of feeding the cables outwards.
Medium-lubricated guide bearings or continuously greased roller bearings are unnecessary because the otherwise usual long drive shaft is omitted completely in this system. The length of the drive shaft is independent of the immersion depth in vertical submersible pumps with canned motor drive.
The application range for the single-stage TCN variants includes delivery heads up to 220 m, volumetric flow rates up to 1,800 m³/h, liquid temperatures of –160 to +250 °C and pressure stages up to 100 bar.
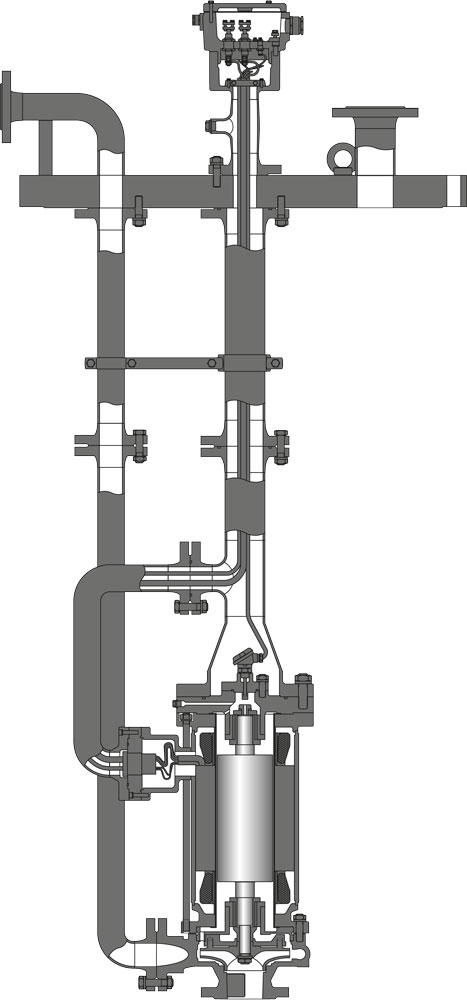
Feeding TDA and ODB (20 bar up to 300 °C) into the reactor (No. 4)
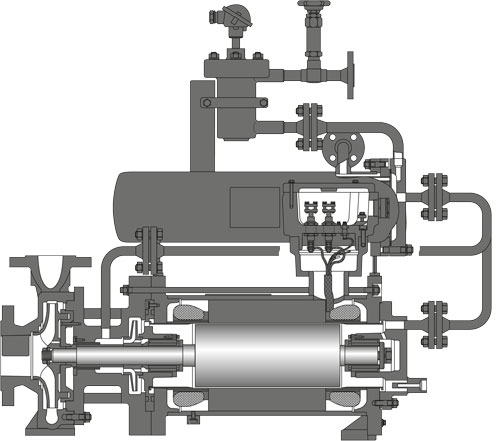
At liquid temperatures of more than 200 °C, HERMETIC offers, with the CNK series, a version of their canned motor pumps which is adapted to the pumping of hot, organic liquids. The pumped liquid passes through the suction compartment into the impeller and is conveyed to the discharge side by this. In this concept, the pump and the canned motor are separated from each other by an intermediate piece which acts as a thermal barrier. This prevents heat from being transferred from the pump to the motor. The motor heat loss is dissipated to a separately arranged heat exchanger through the secondary cooling/lubricating circuit. The pump has been equipped with shell and tube heat exchangers in this application. These are easy to clean and maintain. In the motor itself, an auxiliary impeller is installed which circulates the liquid of the same kind in the rotor chamber by an external tubular cooler arranged around the motor or fitted separately. The motor heat loss is absorbed by a coolant. This creates two delivery circuits with different temperature levels. The operating circuit can be approved for temperatures up to +450 °C, while the pumped liquid of the secondary cooling/lubricating circuit has significantly lower temperatures of +60 °C to +80 °C.
The CNKr series covers a performance range from 1,450 to 3,500 rpm and a pump capacity of 3 to 1,400 m³/h and a delivery head of 3 to 230 m.
Discharge of the raw material TDI from the reactor (No. 6)
In this process step, an extremely dangerous mixture (phosgene), with additional traces of solids, must be pumped. A design was used in the reference plant with the CNPKf which is suitable for pumping contaminated liquids or liquids with traces of solids. This series is produced to standard according to API 685.
One of the target specifications was to minimize the installation effort and avoid adaptations to the piping. A top-top configuration was therefore used in this application. Here, the suction and pressure flanges are designed in vertical alignment in compliance with API. This simplifies laying of the piping and reduces the number of compensating elbows that might be needed. The pumped liquid passes through the suction compartment into the impeller and is conveyed to the discharge port by this. A thermal barrier prevents direct heat transfer from the pump unit to the motor unit. The motor heat loss is dissipated to a separately arranged heat exchanger through the secondary cooling / lubricating circuit. This cooling/lubricating circuit supplies the slide bearings simultaneously. Liquids with a temperature of up to +425 °C can therefore be delivered on the pump side, whilst the secondary cooling circuit is on a lower temperature level.
The CNPKf variants have a performance range of 1,475 to 3,550 rpm with a pump capacity of 3 to 520 m³/h and a delivery head of 7 to 300 m.
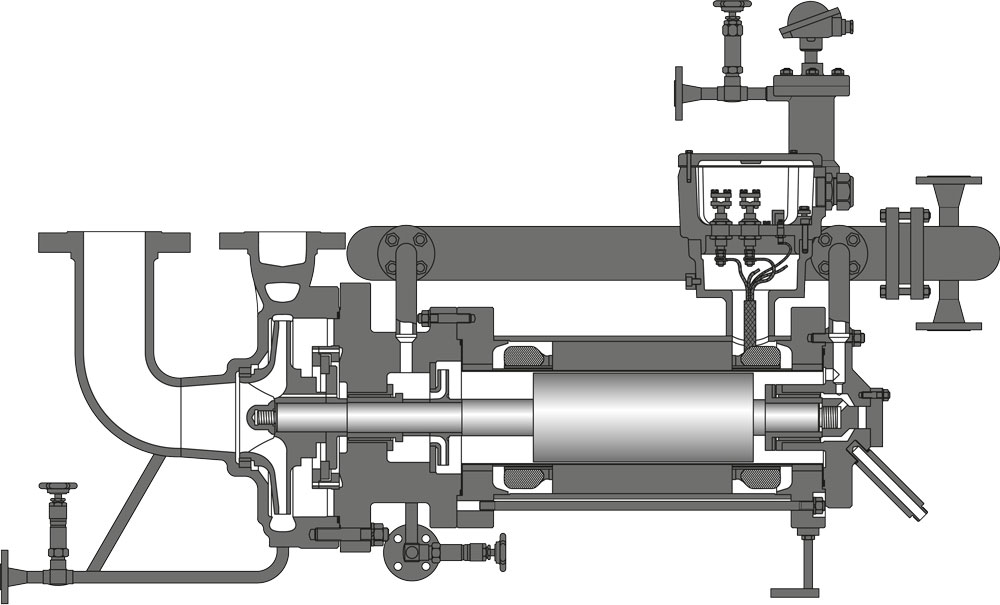
Totally leakage-free, low-wear and low-maintenance pumping technology
Unlike conventional centrifugal pumps with face seals, canned motor pumps manage without any dynamic seals. Instead, they have a second hermetic safety jacket which rules out the escape of pumped media and emissions. The design-related omission of components that are prone to wear such as shaft seals, couplings and roller bearings ensures high operational reliability, almost negligible wear and the best MTBF values (Mean Time Between Failure) compared with other pumping technologies. Every canned motor pump from HERMETIC has highly developed technologies. These include the unique HERMETIC ZART® principle, for example. If the pump is running at the duty point, there is no contact between rotating parts. The complete compensation of the axial forces in connection with hydrodynamic slide bearings guarantees an extremely high reliability in the operator’s processes. This considerably reduces the life cycle and running costs of a canned motor pump.
Sources
- https://www.chemietechnik.de/marktstudie-ammoniak-nachfrage-waechst-dynamisch/
- https://www.persistencemarketresearch.com/market-research/ammonia-market.asp
- Michael Binnewies, Maik Finze, Manfred Jäckel, Peer Schmidt, Helge Willner,
- Geoff Rayner-Canham: Allgemeine und Anorganische Chemie, 2016, Springer Spektrum, ISBN 978-3-662-45067-3 S. 556–561
- http://www.chemie.de/lexikon/Ammoniak.html http://ietd.iipnetwork.org/content/partial-oxidation
- https://www.spektrum.de/lexikon/chemie/sulfosolvan-verfahren/8891
- Jürgen Falbe: Römpp-Lexikon Chemie (H–L), Georg Thieme Verlag, 1997, ISBN 3-13-107830-8, S. 1644–1646
- Detlef Forst, Maximillian Kolb, Helmut Roßwag: Chemie für Ingenieure. Springer Verlag, 1993, ISBN 3-662-00655-3, S. 234–238
- Michael Binnewies, Maik Finze, Manfred Jäckel, Peer Schmidt, Helge Willner,
- Geoff Rayner-Canham: Allgemeine und Anorganische Chemie, 2016, Springer Spektrum, ISBN 978-3-662-45067-3, S. 561
- http://ruby.chemie.uni-freiburg.de/Vorlesung/Gif_bilder/Nichtmetalle/nh3_fliessschema_b.png
Customisation
If you cannot find a suitable pump series? We are happy to help you with a customised solution regardless of the quantity. Please contact us for further information.
Download application report
TDI Applications
Your contact person
For more information, please contact:
Dominik Hegen
Produkt Manager