Sustainable industrial refrigeration system
Compact, resource-saving system concept
Sustainability in refrigeration system construction does not just focus on reducing power consumption and using natural refrigerants. Forward-looking system concepts also impress with their resource-saving design and the right selection of long-lasting components. The refrigeration system manufacturer Holger Andreasen & Partner GmbH shows how this can be achieved using an industrial refrigeration system of the Flux-Hi™ type installed in France. The hermetically sealed canned motor pumps from HERMETIC-Pumpen GmbH also contribute to the sustainable overall concept.
Sustainability is a prevalent and important topic worldwide. This is also the case in the field of refrigeration technology. For improved climate protection, the focus is often on the refrigerant used and the energy efficiency of the system. Natural refrigerants such as ammonia, CO2 or hydrocarbons are playing an increasingly important role in sustainability considerations thanks to their low "Global Warming Potential" (GWP value). Concerning energy efficiency, improved solutions are constantly being sought in system engineering and the individual components. The greatest energy-saving potential of a refrigeration system lies, for example, in preventing deposits in narrow pipes, any unfavourable pipe routing or generally in the compressors. Another, often neglected, key aspect of sustainability is the careful use of resources – especially the consumption of materials. In refrigeration technology, this can be the elimination of additional components, low material wear, or long service and operating life of the system including its components.
Layout of a sustainable refrigeration system
The equipment manufacturer Holger Andreasen & Partner GmbH (HAP) and its customers are also increasingly focusing on sustainability. The company has more than 40 years of experience in shell & tube heat exchangers, pressure vessels and packages for industrial refrigeration and oil & gas applications. In the field of refrigeration technology, Holger Andreasen & Partner develops and builds innovative, advanced solutions, especially in the domain of NH3 and CO2 refrigeration systems. Andreasen & Partner have had enormous success for several years with their specially developed Flux-Hi™ system. The future-proof design of the specially further developed spray chiller now ensures sustainable refrigeration system operation in over 350 installations worldwide as CO2 / NH3 cascade and liquid chillers. This is also the case in an industrial distribution centre for refrigerated food products of a leading supermarket chain in France.
In the NH3 / CO2 cascade system that went into operation in 2021, only natural refrigerants such as ammonia and CO2 are used. The heart of the refrigeration system is the Flux-Hi™ spray chiller. The CO2 is condensed in the Flux-Hi™ cascade while the NH3 evaporates in the same cascade. The CO2 tank below the Flux-Hi™ cascade is operated using pump circulation. Unique hydraulics are used to allocate the NH3 to the Flux-Hi™ cascade and an NH3 heat pump. The Flux-Hi™ volume is also used as a refrigerant separator for the heat pump circuit (see Fig. 1). The installation is designed for a cooling capacity of about 3000 kW and a delta of 3K.
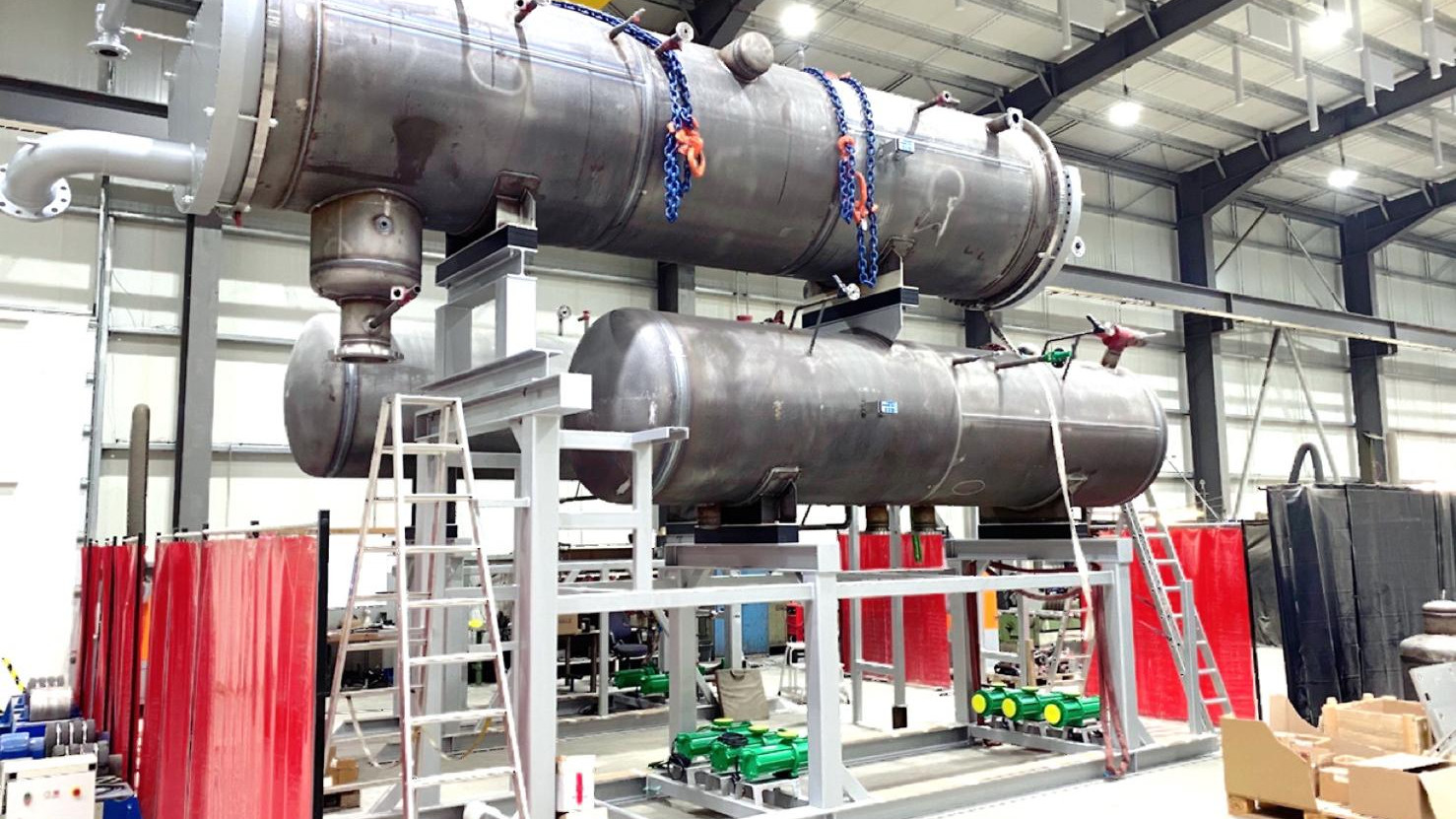
Fig. 1: Layout of the Flux-Hi™ NH3 / CO2 cascade installation in Berlin 2020, Holger Andreasen & Partner GmbH
Resource-saving system concept
On the one hand, the Flux-Hi™ cascade system relies on a compact design without using unnecessary components (see Fig. 2). For example, an additional separator tank is no longer required, since a refrigerant separator is already integrated into the system. On the other hand, the system is designed for sustained operation with low maintenance cycles to make the use of resources as sustainable as possible in the long term. In contrast to conventional plate heat exchangers, any maintenance that is nevertheless necessary can be carried out without shutting down the system for a long time. This is achieved in particular by bolted ends and flange connections meaning that the Flux-Hi™ system can be opened quickly and easily and the tube sheets are accessible.
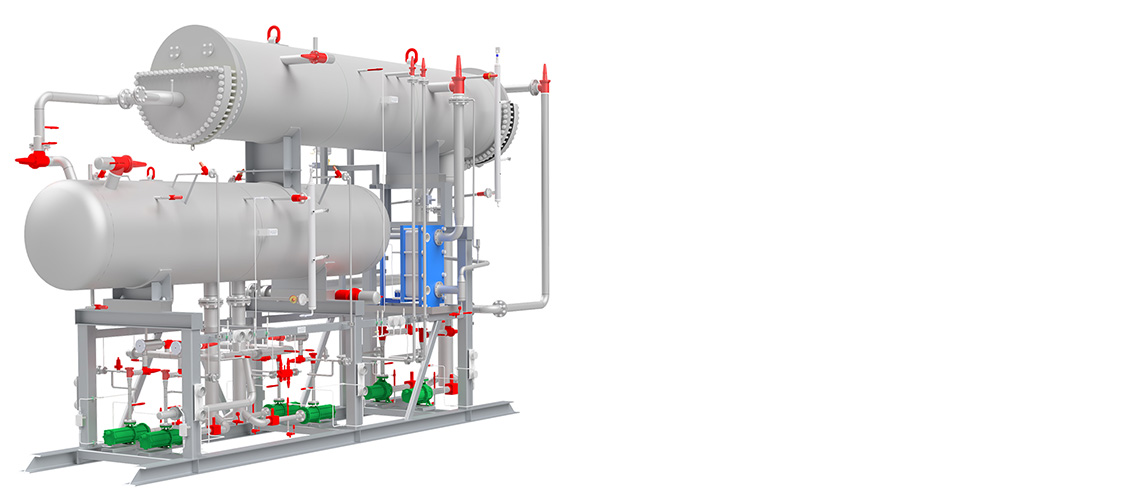
Fig. 2: STEP model of a Flux-Hi™ cascade system, Holger Andreasen & Partner GmbH
Saving of resources when using refrigerants
Another advantage of the system is the sustainable use of refrigerants. Due to the special system design, the refrigerant charge is significantly lower than in other known systems. Only as much ammonia is used as is required for the pump circulation in the spray system. There is no need for an additional filling such as with flooded systems.
To prevent environmental contamination and loss of refrigerant, the connections of the piping to the tube plates are double-sealed in the Flux-Hi™ system and subjected to a helium leak test before delivery. In addition, hermetically sealed canned motor pumps from the Gundelfingen-based pump specialist HERMETIC-Pumpen GmbH are used.
Sustainable pump concept
Eight hermetically sealed canned motor pumps of the types CNF and CAM from HERMETIC are used in both circuits to convey the refrigerants. As core components of the Flux-Hi™ cascade system, the pumps play a major role in the sustainability of the entire system in several respects:
Thanks to their hermetically sealed design and the elimination of couplings between the motor and hydraulics, canned motor pumps not only offer a long service life, but also long maintenance cycles, resulting in exceptionally low material usage over decades. The pumps used still function very often without restrictions even after 40 years of operation.
A single-stage HERMETIC CNF50-200 pump with AGX8.5 motor and inducer circulates the ammonia coming from the separator. A second pump of the same type is on standby for any emergencies. The pump delivers a volumetric flow rate of 45 m3/h with a pumping head of 30 m. The single-stage pump has only one impeller. This type of pump is mainly used when large pump capacities are required at low delivery pressures as in the present case. Thanks to the integrated auxiliary impeller, the single-stage CNF series from HERMETIC (see Fig. 3) is also suitable for liquids with steep temperature-pressure characteristics.
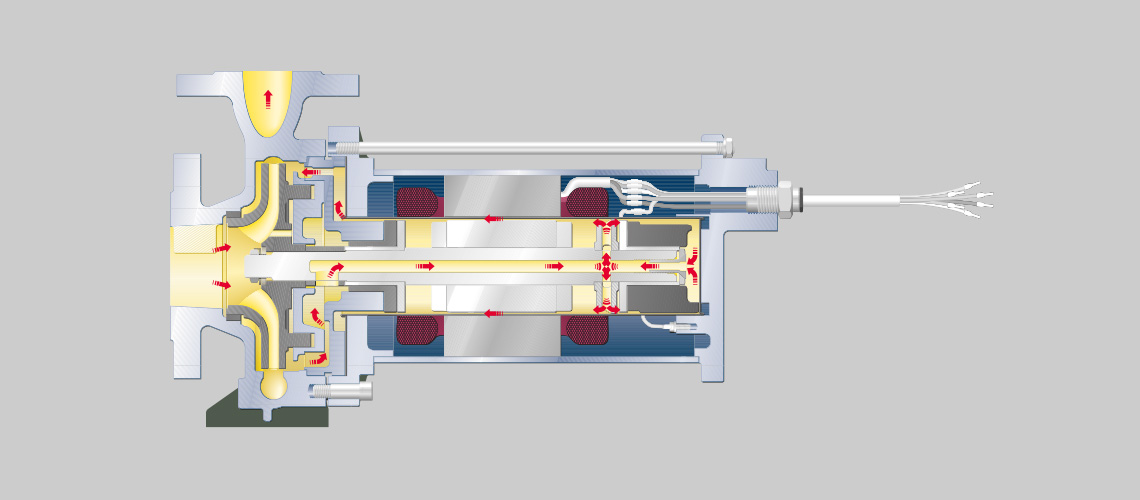
Fig. 3: Single-stage hermetic centrifugal pump of type CNF from HERMETIC-Pumpen GmbH for the ammonia circulation
Six multistage CAM 2/5 pumps with AGX3.0 motors are used to pump the CO2 in the second refrigeration circuit. At full load, these pumps have a cooling capacity of 1830 kW with a pumping head of 45 metres. The multi-stage designs (see Fig. 4) offer the great advantage that the internal pressure build-up allows pumping at high pressure, as in this case with a differential pressure of around 4.5 bar or even higher. All pumps are controlled by frequency inverters to protect the pumps against overloading and ensure the desired operating point.
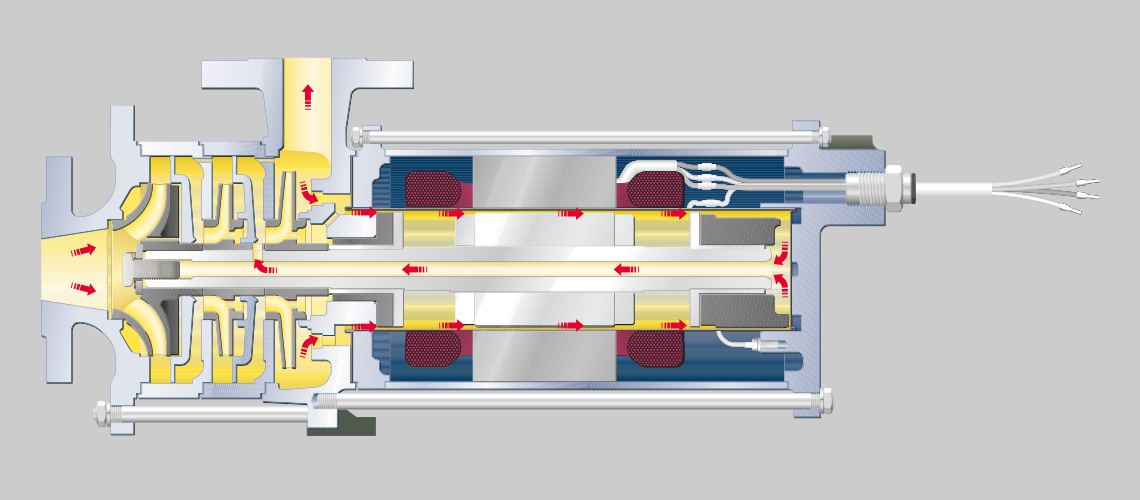
Fig. 4: Multi-stage hermetic centrifugal pump of type CAM / CAMh from HERMETIC-Pumpen GmbH for CO2 circulation
Contribution to saving resources
The secondary containment of the HERMETIC canned motor pumps ensures absolute tightness and more sustainability in terms of refrigerant consumption. The double hermetic containment also protects against environmental contamination. This is of immense importance with toxic refrigerants such as ammonia. Both pump types – CNF and CAM – from HERMETIC are characterised by an excellent delivery rate even at difficult operating points, such as the CO2 delivery circuit in the supermarket system at temperatures below –10°C. Frequency inverters enable the optimal control of the desired operating point for the pumps and the prevention of performance losses. This ensured the energy-efficient operation of the system.
The canned motor pumps also demonstrate their advantages in terms of material consumption: The low NPSHr values of the pumps helped reduce the amount of material used in the piping of the system. While the CAM series can already achieve low NPSHr values thanks to its structural design, the use of inducers in the CNF pumps made it possible to further reduce the NPSHr values. This reduced the size of the refrigeration system and the amount of material used.
High system efficiency
To achieve the best possible energy efficiency of the system, Holger Andreasen & Partner adapts each Flux-Hi™ system to the customer's needs and operating points. For short-term requirements, the refrigeration technology specialist offers the option of using a standardised series (CAS) with short delivery times.
Contact
For more information, please contact:
Adrian Schäfer
Phone: +49 761 5830-343
schaefer.adrian@hermetic-pumpen.com