HERMETIC canned motor pumps –
Safe pump technology for diesel and biodiesel production
The reactor circulation pump pays a decisive role in the catalytic cleaning process in diesel and biodiesel production. The high system pressures and temperatures prevailing in the desulphurisation process demand maximum safety and reliability of the used equipment. The use of catalysts and the fluctuating quality of raw material in biodiesel production present additional challenges. The hermetically sealed design of the HERMETIC pump, extensive measuring and control technology as well as rigorous tests during the test bench acceptance guarantee plant operators a safe pump solution with high availability.
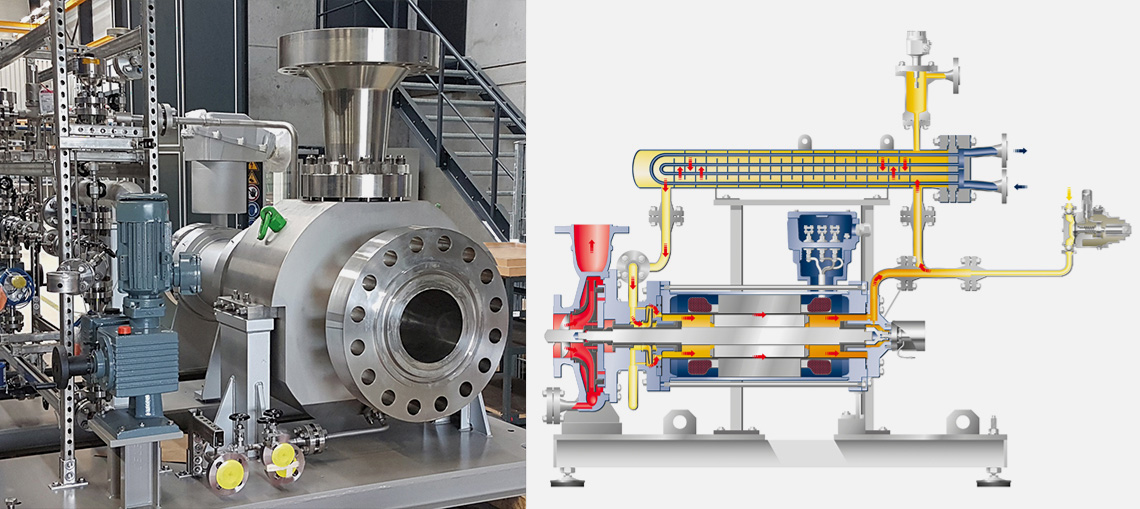
Biodiesel production has become increasingly important in recent years. Whereas about 19.3 billion litres were produced world-wide in 2010, this had become about 40 billion litres by 2020. The global biodiesel production is concentrated on the EU-27, the USA, Indonesia and Brazil, whereby the European Union, with almost 32 % and a production of a good 15.2 million litres in 2021, is by far the most important biodiesel producer world-wide (source: ufop.de1).
Manufacture of biodiesel
Biodiesel refers to fatty acid methyl esters (FAME) which are produced from vegetable oils and animal fats with methanol, for example, by the chemical process of catalytic transesterification and used as fuel for diesel engines. According to ufop, 35 % palm oil, 25 % soya oil and 15 % rapeseed oil are used world-wide. 12 % are accounted for by used cooking fats, 7 % by animal fats and 6 % by “other oils”. Whilst ufop expects that the biodiesel production from soya or palm oil will increase further in North and South America and South East Asia, the percentage of biodiesel from waste oils and fats is expected to increase in the EU-27. In the transesterification process, the high-molecular triglycerides of oils are broken down with the aid of a catalyst and transformed into lower molecular fatty acid methyl esters by addition of methanol. Glycerine is produced as a by-product.
The catalytic cleaning process
As in the production of diesel fuel, the catalytic cleaning and sulphur reduction are decisive steps in the manufacture of biodiesel to satisfy the necessary quality standards. In addition to the elimination of contaminants such as free fatty acids, water, alcohols, pigments and heavy metals, an efficient sulphur reduction is essential. This is typically achieved by the use of catalytic hydro-treating processes. Hereby, the biodiesel – in exactly the same way as in diesel production – is treated with hydrogen in the presence of a suitable catalyst to remove the sulphur compounds. System pressures of more than 100 bar and temperatures of above 400 °C have to be dealt with in this process.
High demands on the reactor circulation pump
The reactor circulation pump plays a decisive role in the sulphur reduction. The recirculation pump is responsible for the continuous flow of biodiesel through the catalytic reactor. It ensures that the biodiesel comes into uniform contact with the catalyst and an efficient reaction is enabled. In addition, the recirculation pump helps to keep the temperature in the reactor constant and maximise heat transfer effects.
The high temperatures and the aggressiveness of the chemicals demand high corrosion resistance and tightness of the equipment. Since even the slightest leakage can cause fatal fires, plants and components are subject to maximum safety and reliability demands. The pump must also be able to cope with the high pressure in the system to ensure a continuous flow of the biodiesel. Since canned motor pumps are hermetically sealed and offer a high level of safety, they are particularly well suited to this purpose. Unlike conventional centrifugal pumps with mechanical seals, caned motor pumps manage without any dynamic seals. Instead, they have a second hermetic safety sleeve which rules out the escape of pumped media and therefore emissions to the environment. A pump with a mechanical seal, on the other hand, poses an increased risk of self-ignition and a high fire risk due to seal leakages.
Leakage-free, safe pump solution for a wide application range
HERMETIC canned motor pumps of the CAMKfH+D type, with their closed, leakage-free design, offer the optimum solution for reactor circulation in the catalytic cleaning process.
The CAM series is suitable for the safe pumping of aggressive, toxic, hot, explosive, valuable and inflammable liquids as well as liquid gases. In the high-pressure version, high system pressures (up to 1,200 bar) can be managed in a technically simple way. The wall thicknesses of the outer components correspond to the required pressure rating. The high-temperature version with external cooling of the pump allows the use of media up to +400 °C. Heat exchangers are used as standard for these pumped media (with ASME certification on request) but compact brazed heat exchangers or air coolers are also available depending on national pressure equipment directives. Since, with the use of catalysts, particles or flocculation can form in the process fluid, for example due to ageing of the catalyst, the pump has a dosing pump. In order to prevent possible engine and bearing damage, a fine, even counterflow is generated by a dosing pump adapted exactly to the application with the aid of the pure pumped medium in the rotor compartment which prevents this.
The range of applications for CAMKfH variants includes pumping heads of up to 500 m, volumetric flow rates of up to 600 m³/h, fluid temperatures from –120 °C to +400 °C, power ratings of up to 700 kW and pressure ratings of up to 450 bar.
In an example plant, a six-stage canned motor pump of the CAMKfH+D 44/6 type operates at a delivery rate of 56 m³/h and a pumping head of 430 m. The NH75zx-2 motor has a shaft power of 138 kW. The operating temperature is 232°C, the steam pressure 117 bar.
Compact, low-wear and low-maintenance design, low life cycle costs
The presence of solids such as catalysts may pose a serious challenge to the mechanical seal used in standard chemical pumps. The design of canned motor pumps omits components that are prone to wear and failure such as shaft seals, couplings and roller bearings to achieve high operational reliability, almost negligible wear and best MTBF values (Mean Time Between Failure) compare with other pump technologies.
The integral and compact block design makes shaft alignment superfluous. There is therefore no need for a mechanical coupling and coupling guard as well as the often complex base plate design. The pump and motor are continuously aligned preventing vibration due to thermal expansion and the associated damage to bearings.
Complete system including control and monitoring technology
Biodiesel is often produced in batch processes. The raw materials for the biodiesel may be available in different quantities and different qualities which can lead to respective different resistances in the catalytic cleaning process. The rotational speed of the HERMETIC caned motor pump can be adapted accordingly due to its suitability for operation on the frequency converter.
The HERMETIC technology "ZART" (Zero Axial and Radial Thrust) ensures that the rotor unit runs without contact and wear. It is based on comprehensive axial thrust balancing in conjunction with hydrodynamic sleeve bearings. While relief mechanisms in the control unit continuously monitor the axial position of the pump shaft, a fine fluid film between the rotating and static sleeve bearing component allows a full "floating" of the rotor. The axial thrust balancing is monitored by the “MAP” rotor position monitoring. It detects the slightest plays in the rotor movement and serves as a kind of early warning system to prevent undesired operating conditions and expensive damage. Thanks to this hydraulic force balance, the HERMETIC pump operates without radial and axial wear and therefore offers plant operators much longer service lives at lower life cycle costs.
In this pump system, an external heat exchanger ensures the dissipation of motor heat loss, whilst a heat barrier prevents the heat transfer from the pump to the motor part. To prevent overheating, a temperature monitoring of the motor winding is integrated. Another sensor monitors the temperature of the motor cooling circuit, which ensures the cooling performance and the functional safety. Other components such as safety valves, rigorous test and inspection processes including X-ray inspections, vibration tests and ultrasonic tests as well as extensive documentation complete the scope of supply for an extremely reliable system. HERMETIC pumps prove their safety and performance capability in diesel and biodiesel refining world-wide.
1 ufop: Union zur Förderung von Öl- und Proteinpflanzen e.V., Report on the Global Market Supply 2022/23, www.ufop.de (Access date: 04/06/2023)
HERMETIC-Pumpen GmbH
HERMETIC-Pumpen GmbH is a worldwide leading developer and manufacturer of hermetic pumping technologies. As a canned motor pump specialist, HERMETIC has gained a reputation worldwide for safe and durable pumps – for the most extreme areas of application and most hazardous pumped media. HERMETIC canned motor pumps are suitable for fluid temperatures ranging from –160 °C up to +480 °C and system pressures up to 120 MPa. With power outputs from 1 kW to 690 kW, HERMETIC offers canned motor pumps with the highest capacities on the market. HERMETIC employs around 440 people at its headquarters in Germany and has subsidiaries in China and the USA. In conjunction with a worldwide service and contract partner network, the company offers reliable customer service over the entire life cycle of a system.